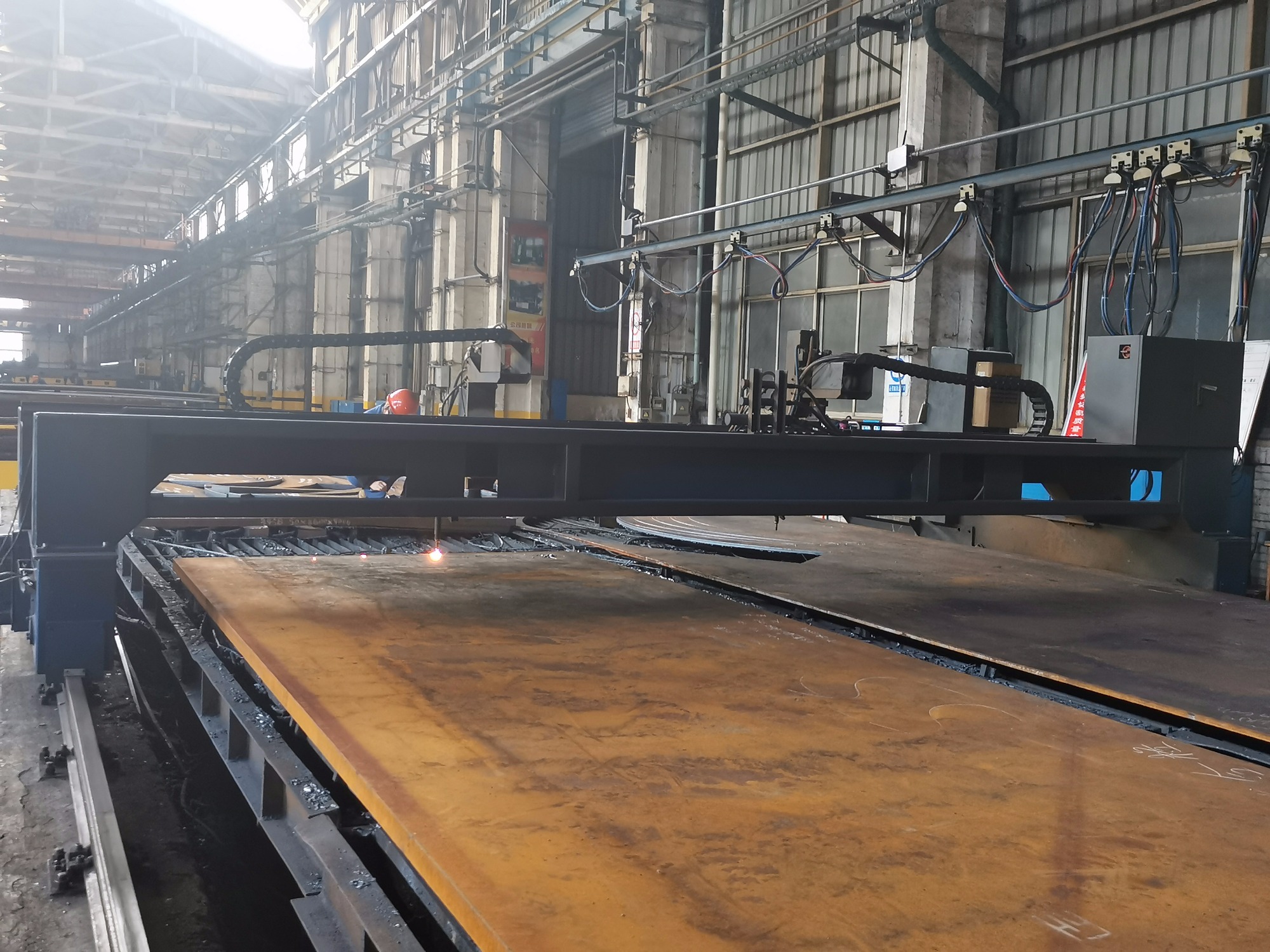 |
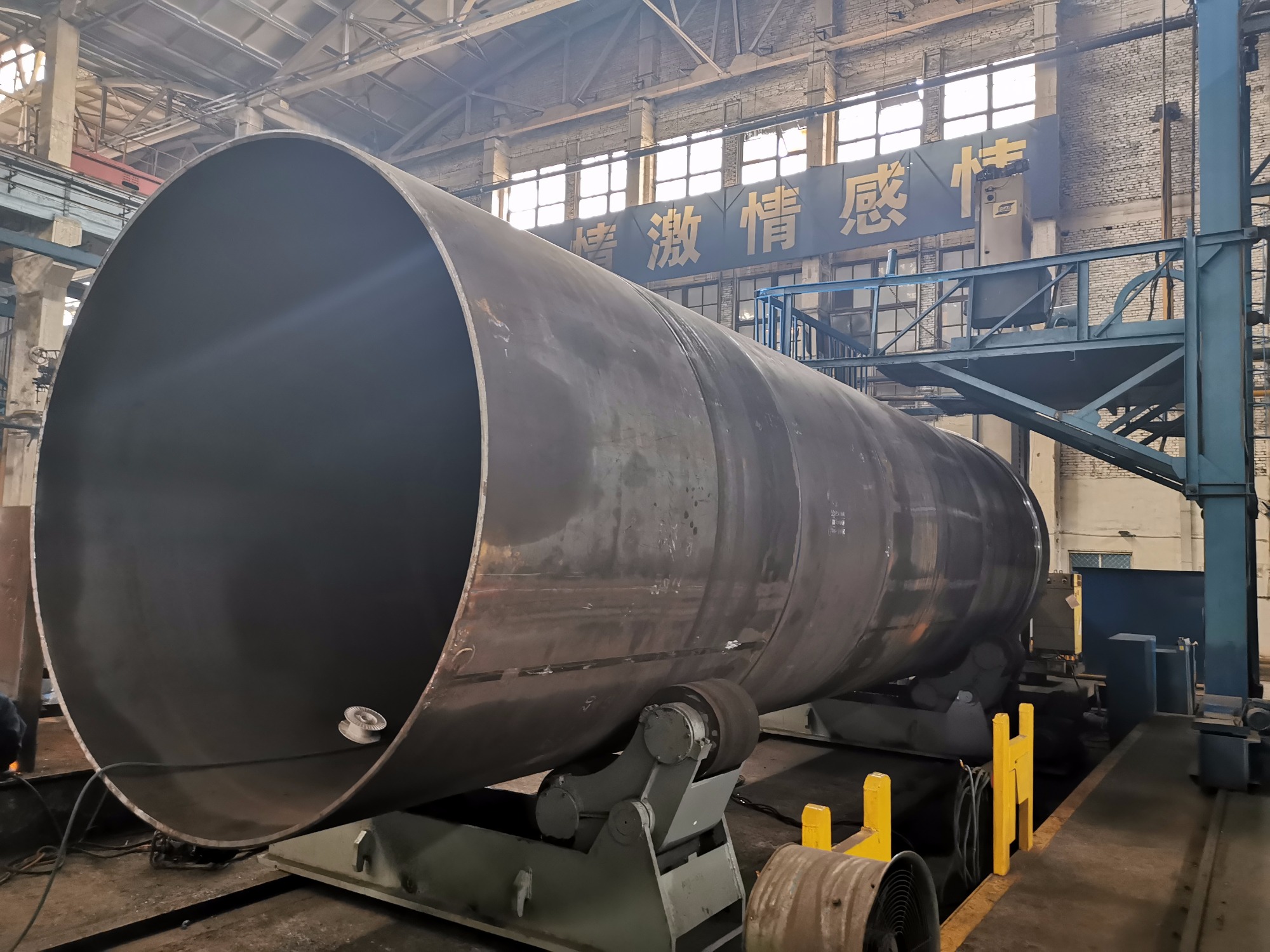 |
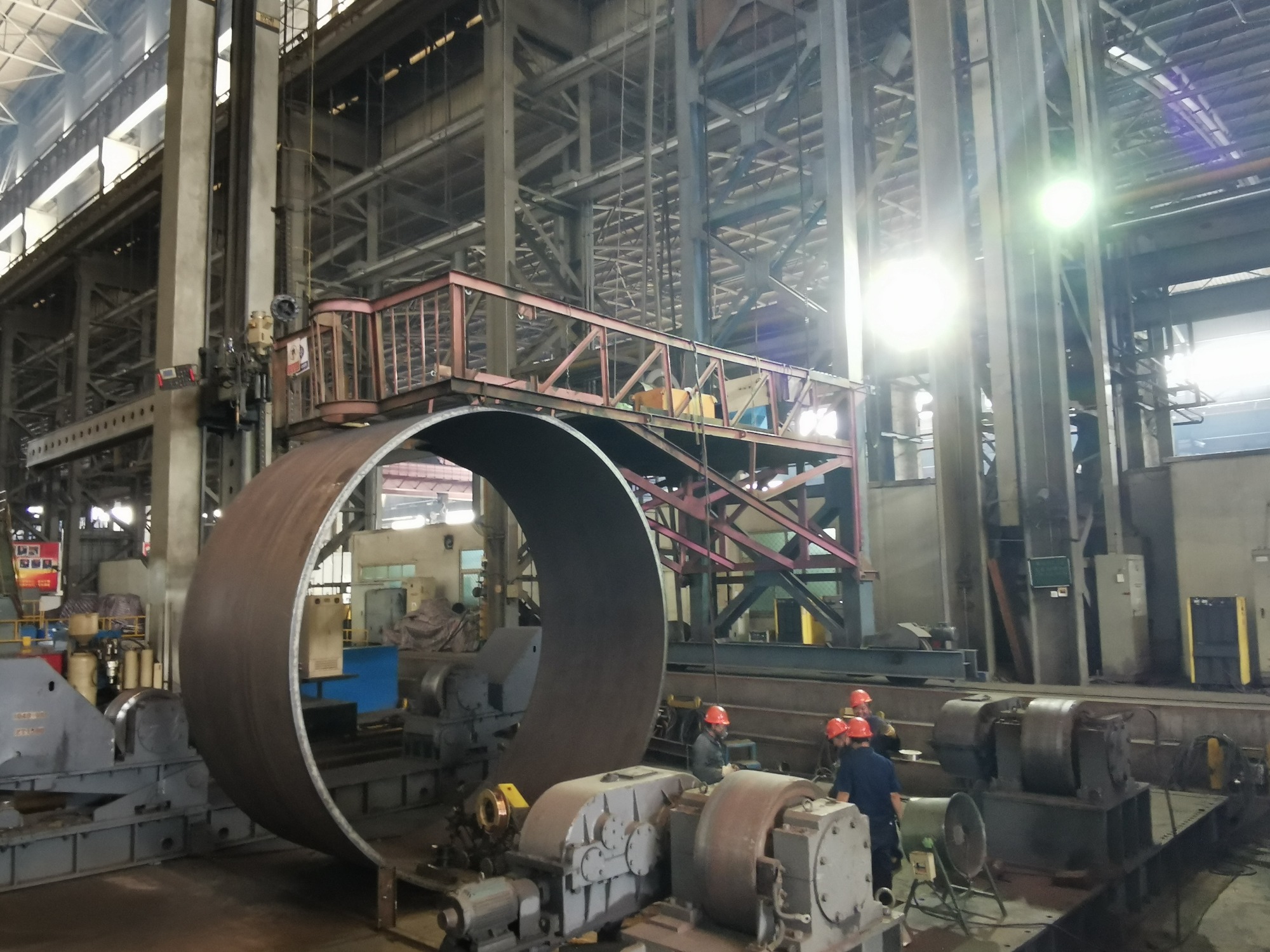 |
1.Grinding Mill Shell Base Plate |
2.Cement Mill Shell1 |
3.Φ6.7×3.2m SAG Mill Shell |
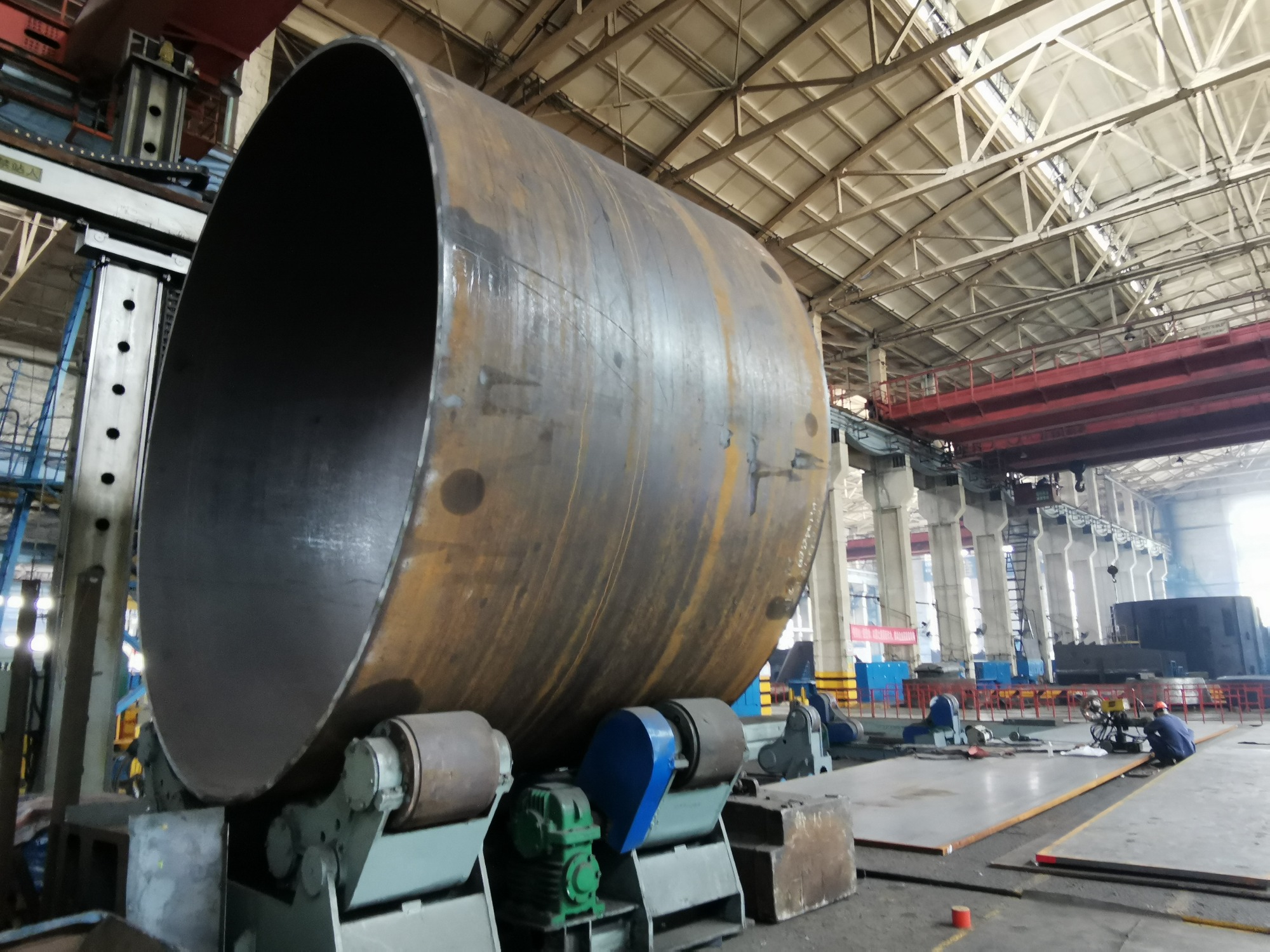 |
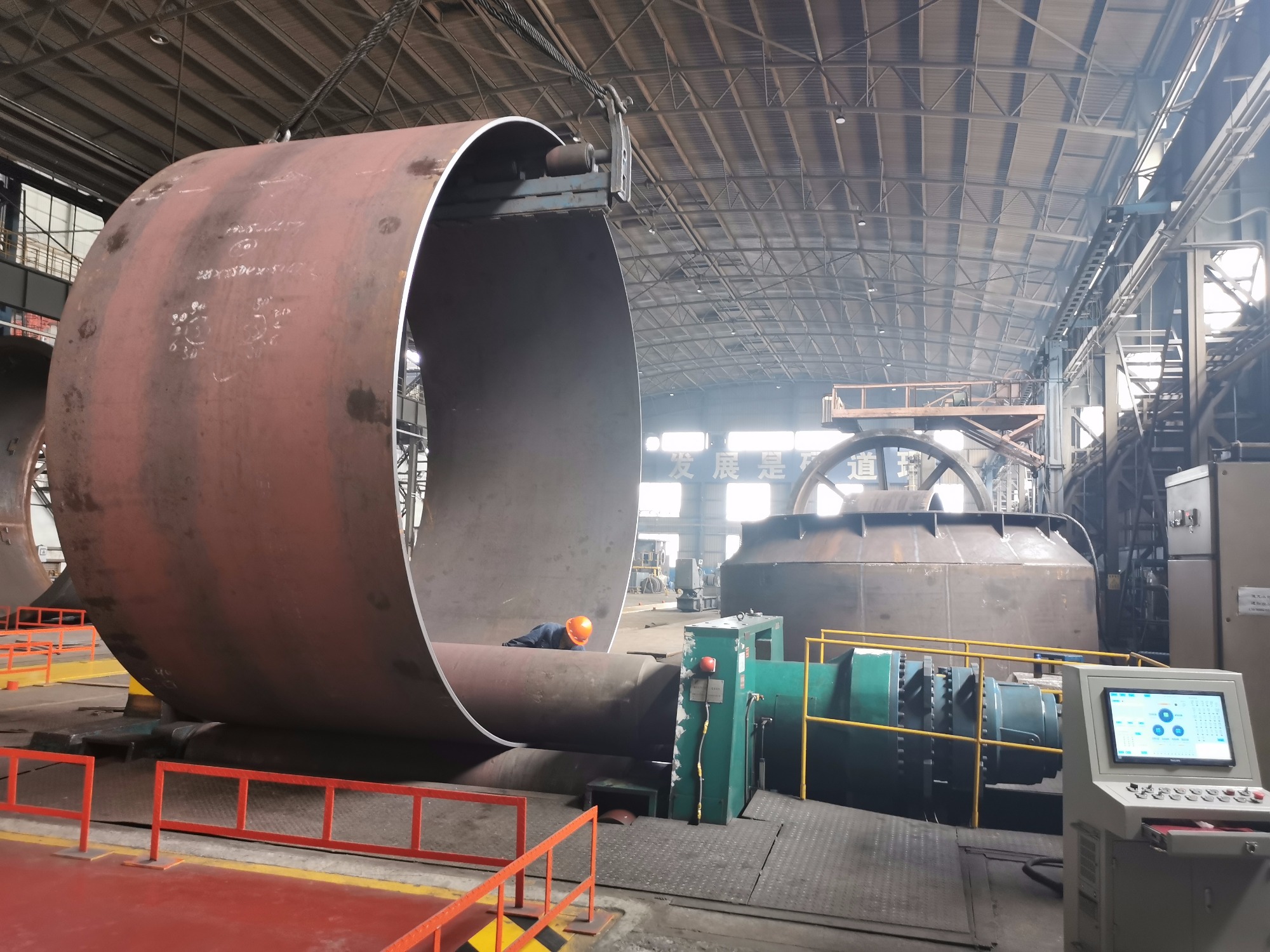 |
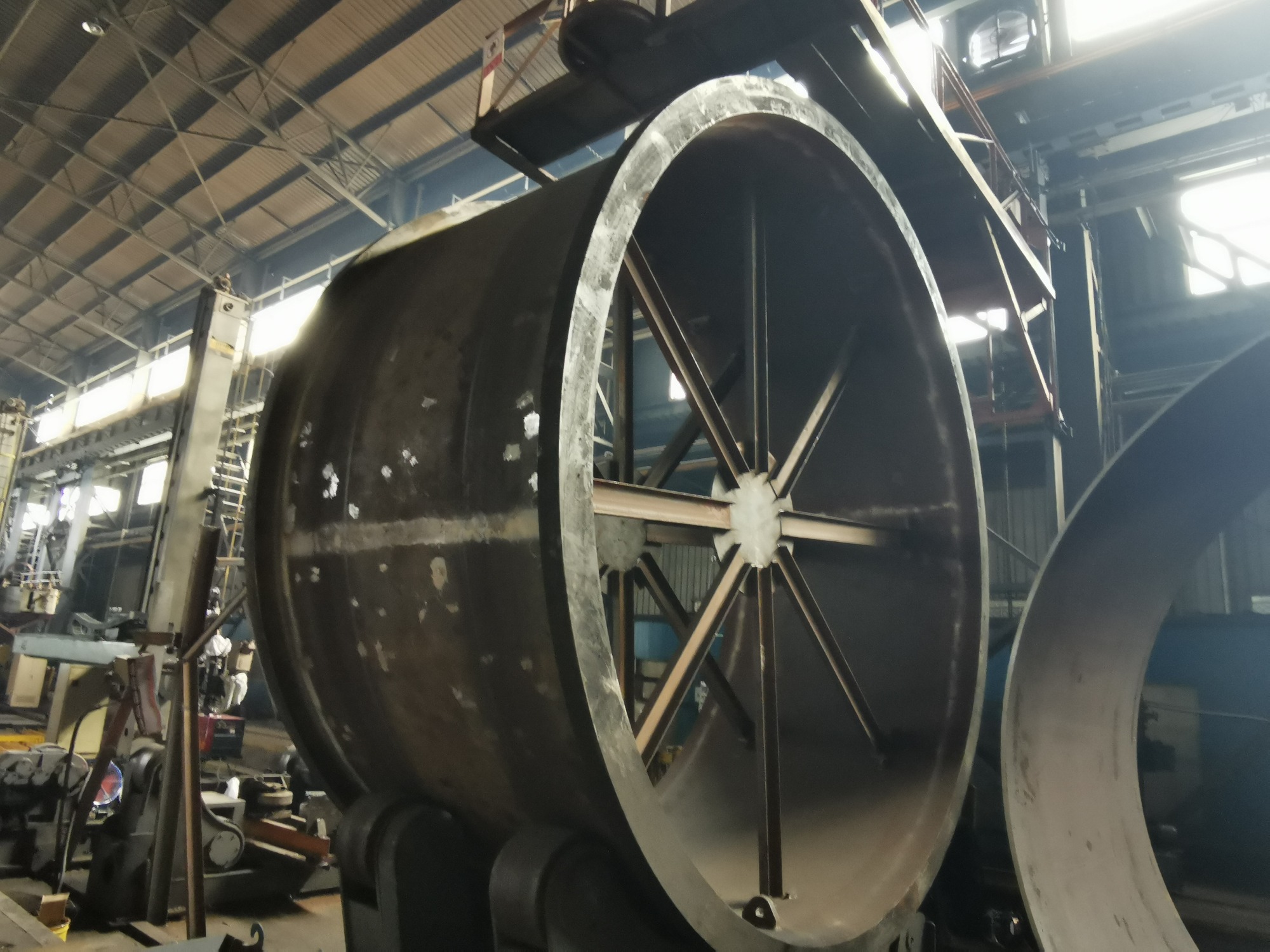 |
4.Φ7×3.5m SAG Mill Shell |
5.Grinding Mill Shell Reel |
6.Welding of Mill Shell Flange |
1. Manufacturing Technology
1.1 Grinding Mill Shell structure: integral, segmented, segmented flange bolt connection, with cylindrical support, hoisting device.
1.2 Grinding Mill Shell Manufacturing Process
Welding→ Mill Shell blank inspection→Mill Shell flange finishing→Mill Shell end flange connecting hole and cylindrical liner hole processing→Mill Shell final correction→ Marking→ Anti-rust.
1.3 Grinding Mill Shell Welding Technology
Base Material Preparation→ Assembly →Shell Support →Weld Blasting Stress Release →Nondestructive Testing
2.Testing
2.1 Base Material Testing
The reported results of Mill Shell materials shall conform to ASTM A36 standard and grade. The maximum carbon content should not exceed 0.30%. Other materials should meet this standard. In addition, all base metal steel plates, whether Mill Shell or flange, should be inspected continuously on steel plates at 75mm intervals perpendicular to the rolling direction in accordance with ASTM A578 "Standard Specification for Ultrasound Inspection of Straight Probes for Special Application Steel Plates", and the quality of which should be determined by the steel mill or manufacturer according to the discontinuity without flake or inclusion bundle or strip type. Tai Ge. Corresponding standards refer to AS1710200. This specification also divides the quality grade of steel plate into grade 1.
2.2 Weld Testing
Magnetic particle (MT) inspection standard: According to ASTM E1444 - magnetic particle inspection standard, 100% magnetic particle inspection was carried out on all welds.
Ultrasound (UT) flaw detection standard: According to ASTM A435 standard, all welds should be 100% ultrasonic flaw detection.