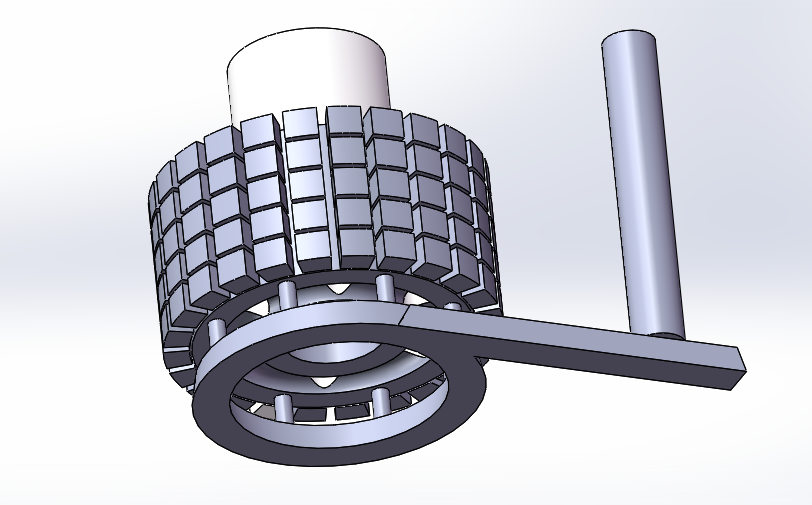 |
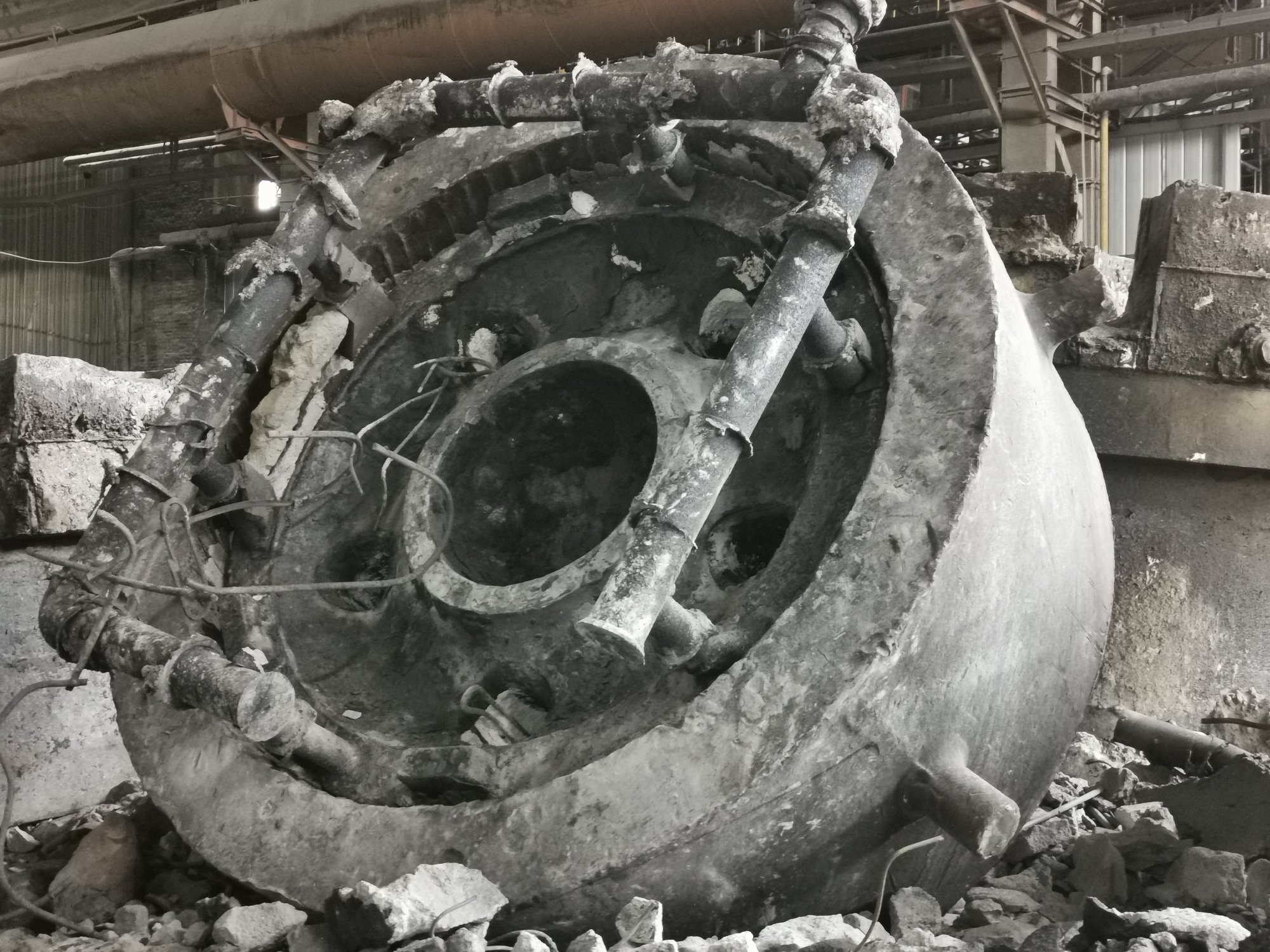 |
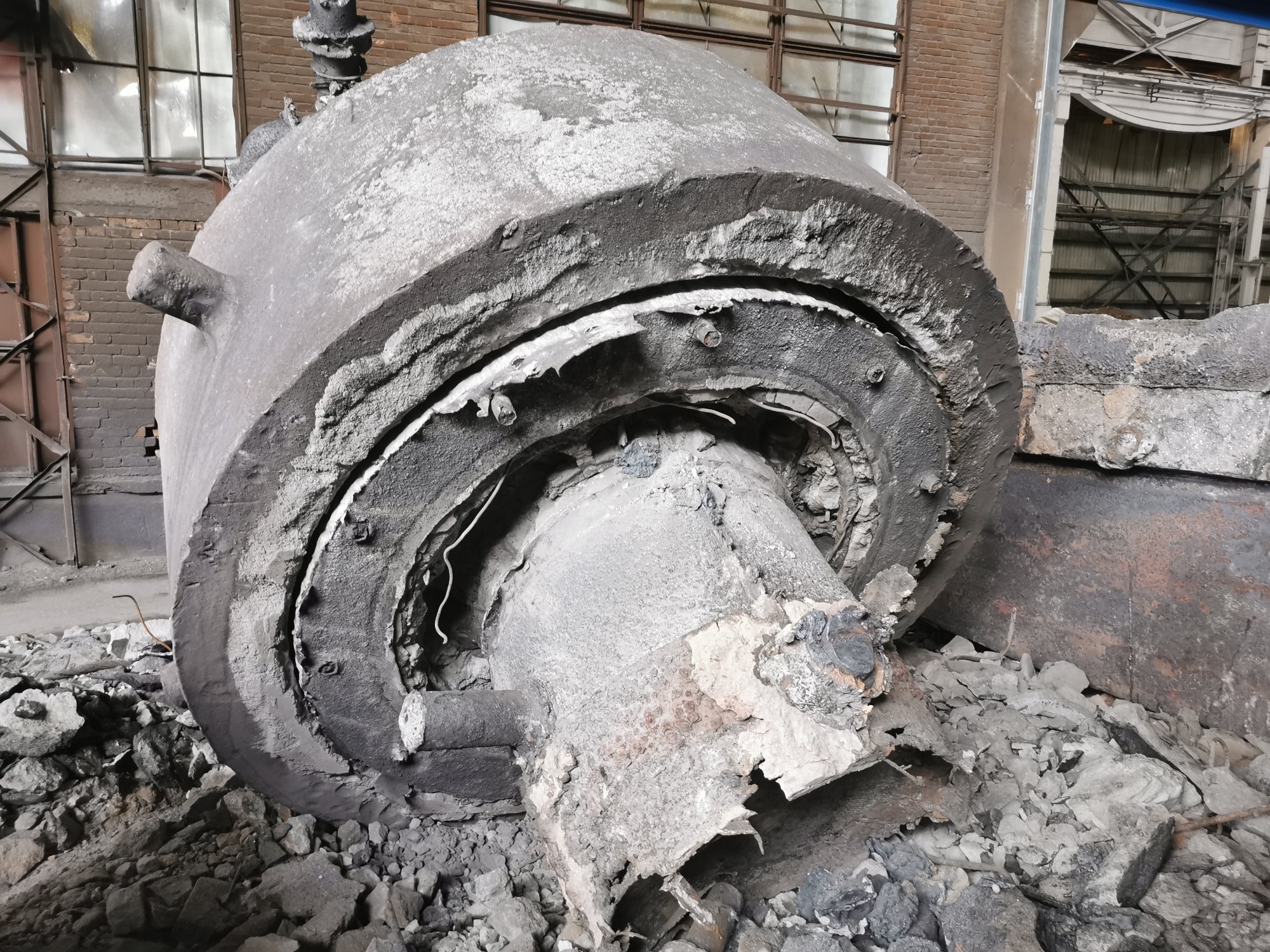 |
1.Cast Steel Support Rollers Casting Technology
|
2.Cast Steel Support Rollers Casting-1
|
3.Cast Steel kiln Support Roller Casting-2
|
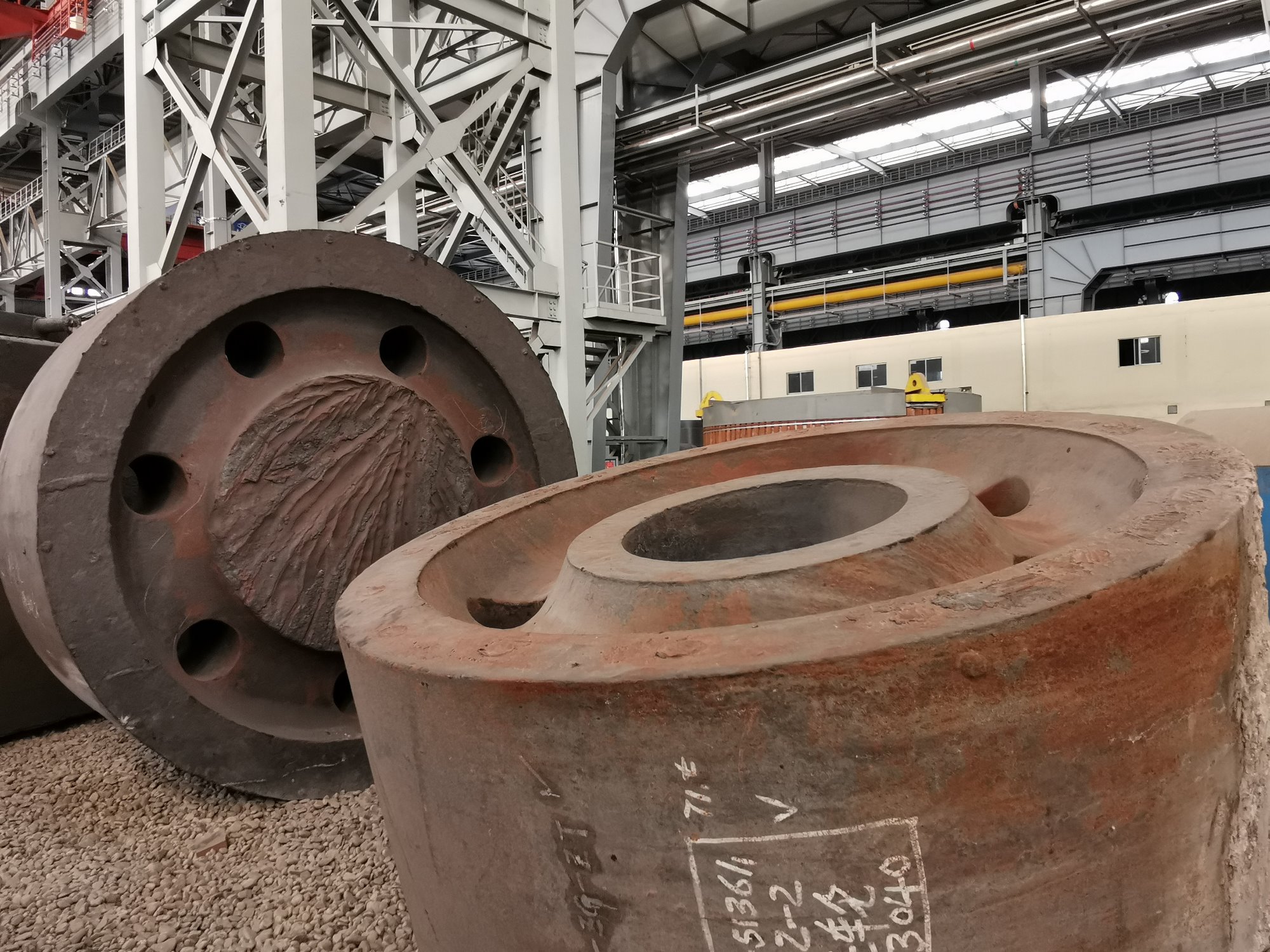 |
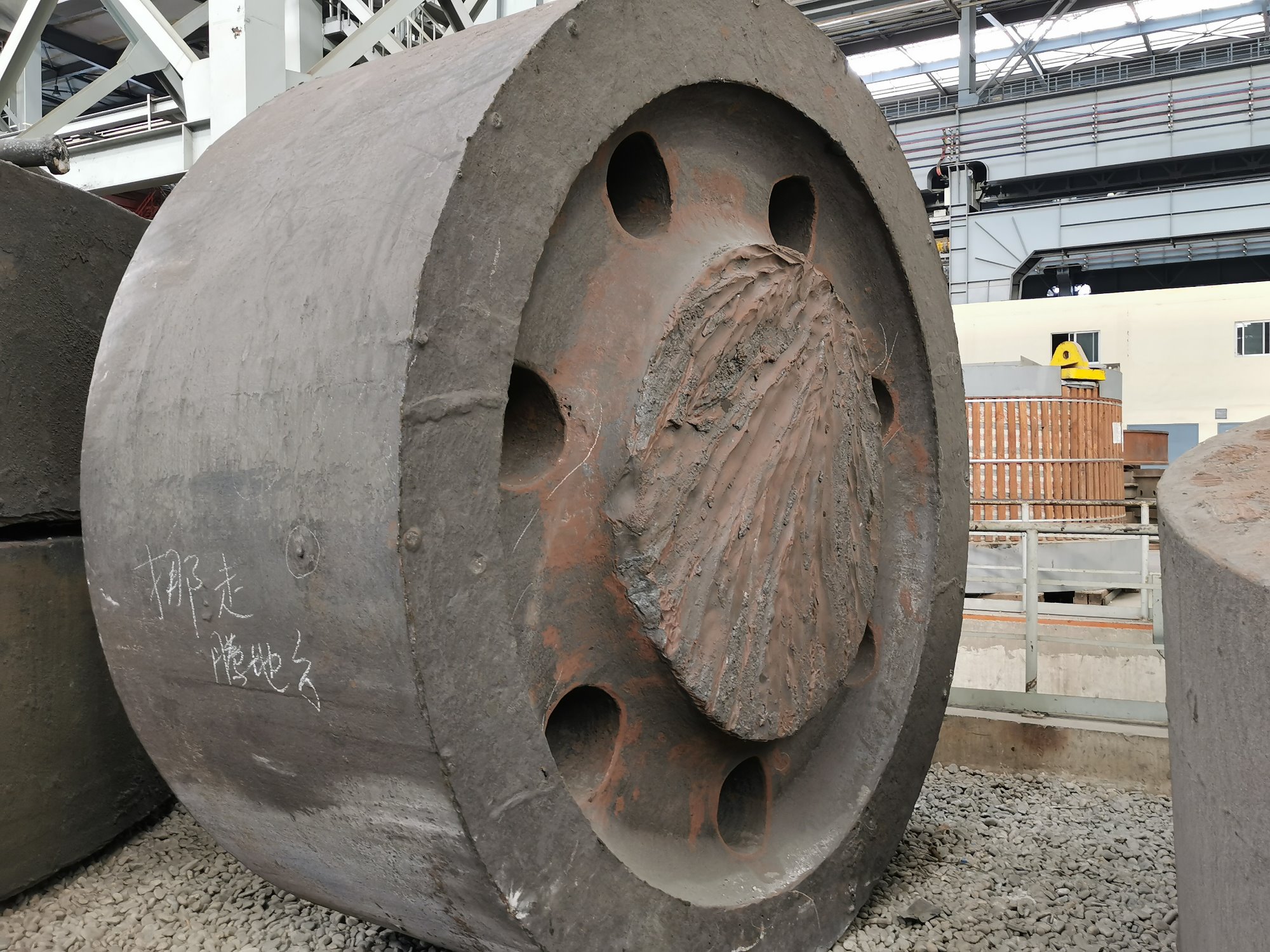 |
|
4.Cast Steel Support Rollers Roughcast-1 |
5.Cast Steel Support Rollers Roughcast-2 |
|
Support Rollers Sdevice bears all the weight of the rotary part (including cylinder, material, feed plate, wheel belt, girth gear, etc.) and positioning the cylinder in the radial direction. Because the Support Rollers device of rotary kiln has the characteristics of heavy load, poor working environment, continuous operation, time-consuming and labor-consuming maintenance, etc. Characteristic, therefore, the quality of Support Rollers is very important. The Support Rollers device consists of a pair of Support Rollers, four pairs of bearings and a large base. The selection of Support Rollers device is very important. The good Support Rollers selected by rotary kiln manufacturers can prevent users from having too many problems in the operation process. Generally, large Cement kiln Support Rollers with thicker wall than 300 mm choose more cast steel. For the Support Rollers of rotary kiln, we adopt the following standards to achieve high quality.
■ Material and Chemical Composition
|
|
|
|
|
|
|
|
|
|
Chemical Constituents |
Table 1 (wt%) |
|
|
|
|
|
Steel Grade |
C |
Si |
Mn |
|
P |
S |
Cr |
Mo |
|
|
|
|
|
|
|
|
|
ZG42CrMo |
0.38~0.45 |
0.3~0.6 |
0.6~1.0 |
|
≤0.030 |
≤0.030 |
0.8~1.2 |
0.2~0.3 |
|
|
|
|
|
|
|
|
|
■ Mechanical Properties
|
Mechanical properties should be in accordance with Table 2. |
|
|
|
|
|
|
|
|
|
|
|
|
|
|
|
|
|
|
|
Steel No. |
Heat Treatment Status
|
|
σb |
|
σs |
δ5 |
ψ |
Hardness |
|
|
MPa |
|
MPa |
% |
% |
HB |
|
|
|
|
|
ZG42CrMo |
|
|
≥690 |
|
≥490 |
≥12 |
≥20 |
≥200 |
|
Quenching and tempering
|
|
|
|
|
|
|
|
|
|
|
≥569 |
|
≥343 |
≥12 |
≥20 |
≥200 |
|
|
|
|
|
|
Normalizing + tempering
|
|
|
|
|
|
|
|
|
■ Casting
Electric furnace smelting is generally required, and other smelting methods to ensure quality can also be adopted with the consent of the orderer. All operation steps and parameters (pouring temperature, pouring time) must be recorded during the whole casting production process.
■ Heat Treatment
The required mechanical properties can be obtained by normalizing and tempering, or by quenching and tempering heat treatment. The heat treatment process parameters such as heating temperature, heating speed, holding time, cooling form and speed should be strictly in accordance with heat treatment.
■ Chemical Composition Analysis
Chemical composition analysis should be carried out according to the method specified in GB/T 223 or other methods that can ensure the quality of analysis.
The chemical composition of molten steel in each furnace (each ladle) can be determined by sampling in front of the furnace. The chemical composition of molten steel in each furnace (each ladle) should be recorded separately in multi-furnace joint casting.
■ Testing of Mechanical Properties
Samples used for mechanical properties testing should be tested after heat treatment. The test method and sampling were carried out in accordance with the requirements of GB/T 228 and GB/T 229. If the orderer specifies the sampling location and test method in the technical agreement, it shall comply with the requirements of the orderer.
■ Hardness Test
After roughing or secondary heat treatment, the hardness of Cement kiln Support Rollers
and retaining wheel is tested. The hardness test shall be checked and accepted according to the technical requirements of the drawings; if the hardness deviates from the stipulation, it must be consulted with the design department. Detection location is performed according to ITP regulations.
■ NDT
The chemical composition and mechanical properties of the castings should be checked and recorded. Cracks, blowhole and slag inclusion are not allowed before the delivery of the blank. If the defects can be removed after processing, they can not be treated.
◆ Roughcast Inspection
Ultrasound flaw detection after rough processing shall be carried out in accordance with GB/T 7233-2009 Standard Class II or III. If the manufacturer's requirements for manufacturing and inspection of rotary kiln supporting and retaining wheels are higher than this standard, they shall be carried out according to the technical requirements of the orderer.
◆ Ultrasound Flaw Detection
After finishing, magnetic particle inspection shall be carried out on the machined surface of the parts according to the regulations of GB/T 9444-2007 grade II or III.
◆ Magnetic Particle Detection
■ Welding repair
Defect removal and welding repair process should be carried out according to JB/T 5000.7-2007 or according to welding repair process, after welding repair inspection.
◆ Magnetic Particle Inspection
All welding repair areas are inspected by magnetic particle inspection according to the quality requirements of castings.
◆Ultrasound Flaw Detection
All welding areas are inspected by ultrasonic inspection according to the quality requirements of castings, and repairing by filling is strictly prohibited.
◆ Hardness Inspection of Welding Repair Zone
The hardness value of the area near the welding repair area is strictly prohibited to exceed the hardness value of base metal above 50HB. If the hardness can not meet the requirements, heat treatment must be repeated.