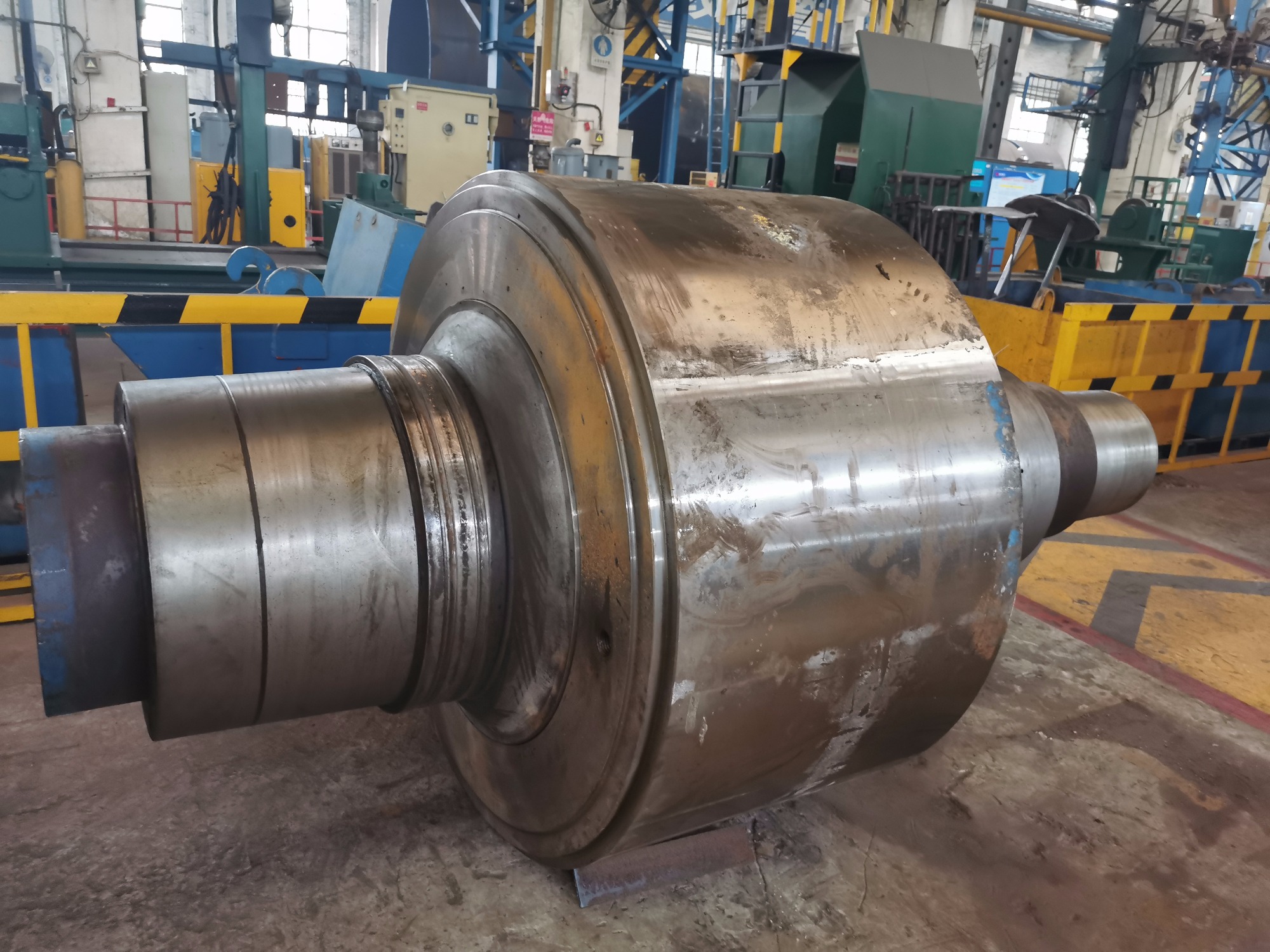 |
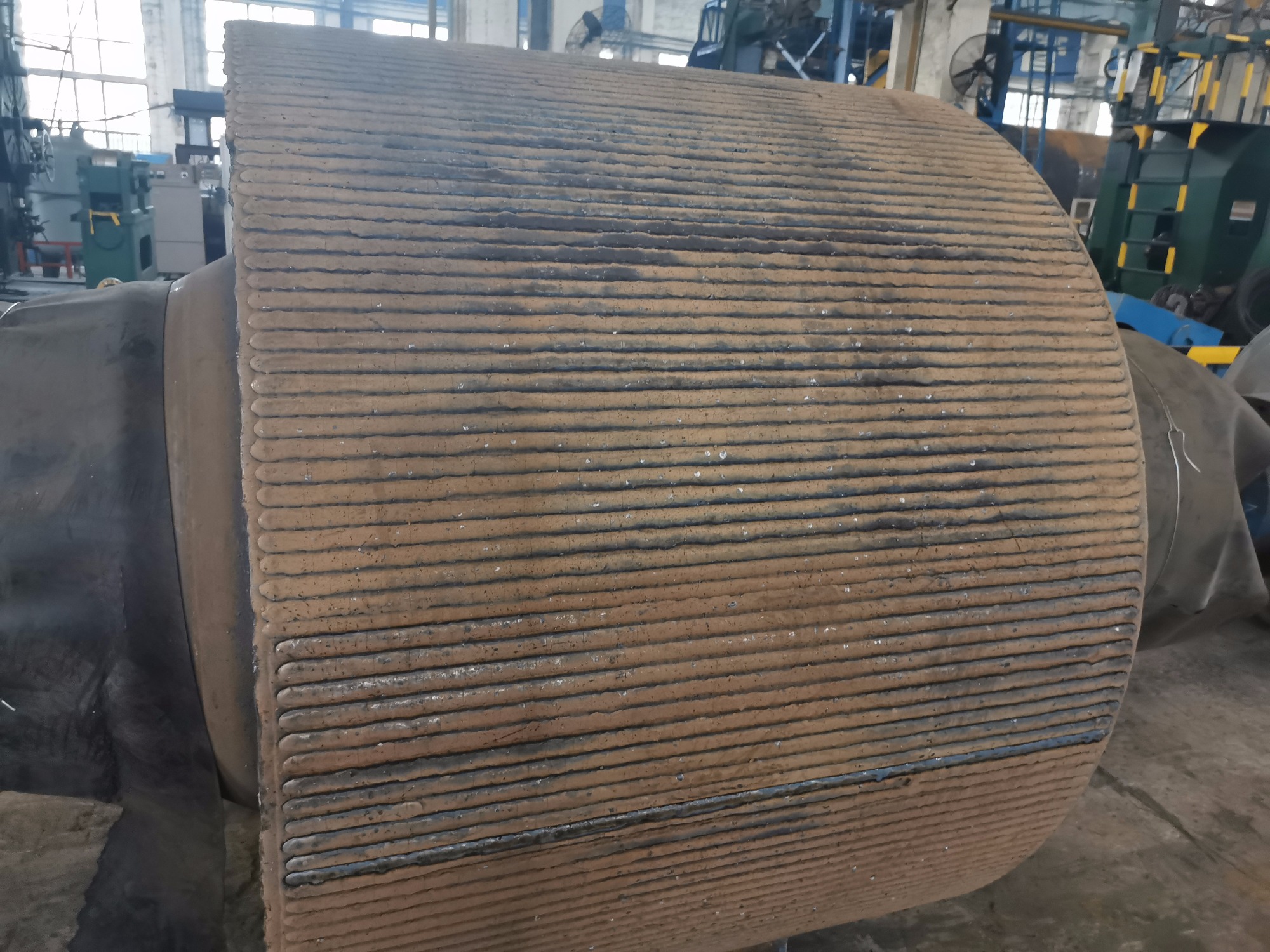 |
1.Extrusion Roll of RP170-120 High Pressure Roll Mill
|
2.Surfacing Wear Resistant Layer of Extrusion Roll of RP170-120 High Pressure Roll Mill |
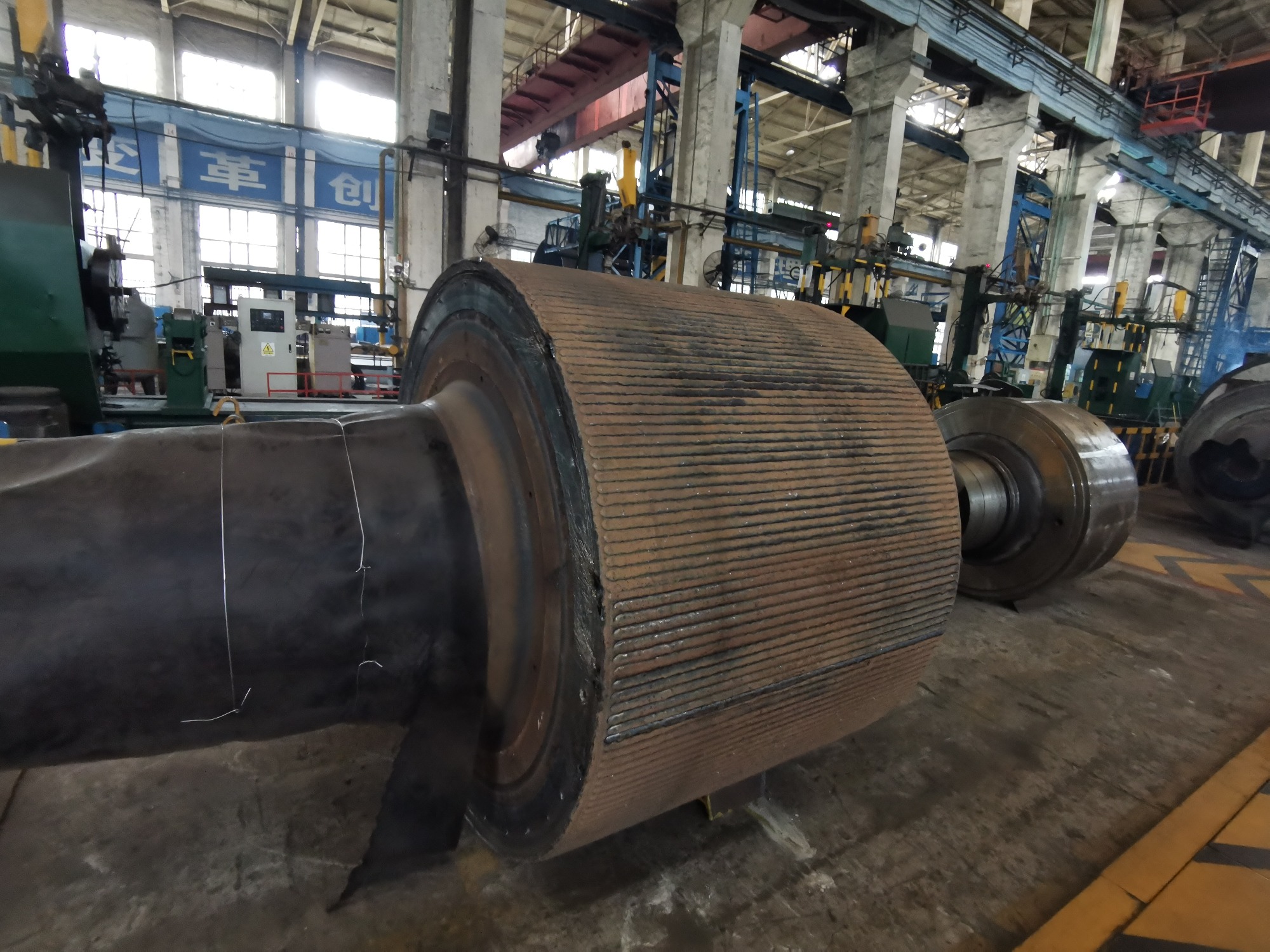 |
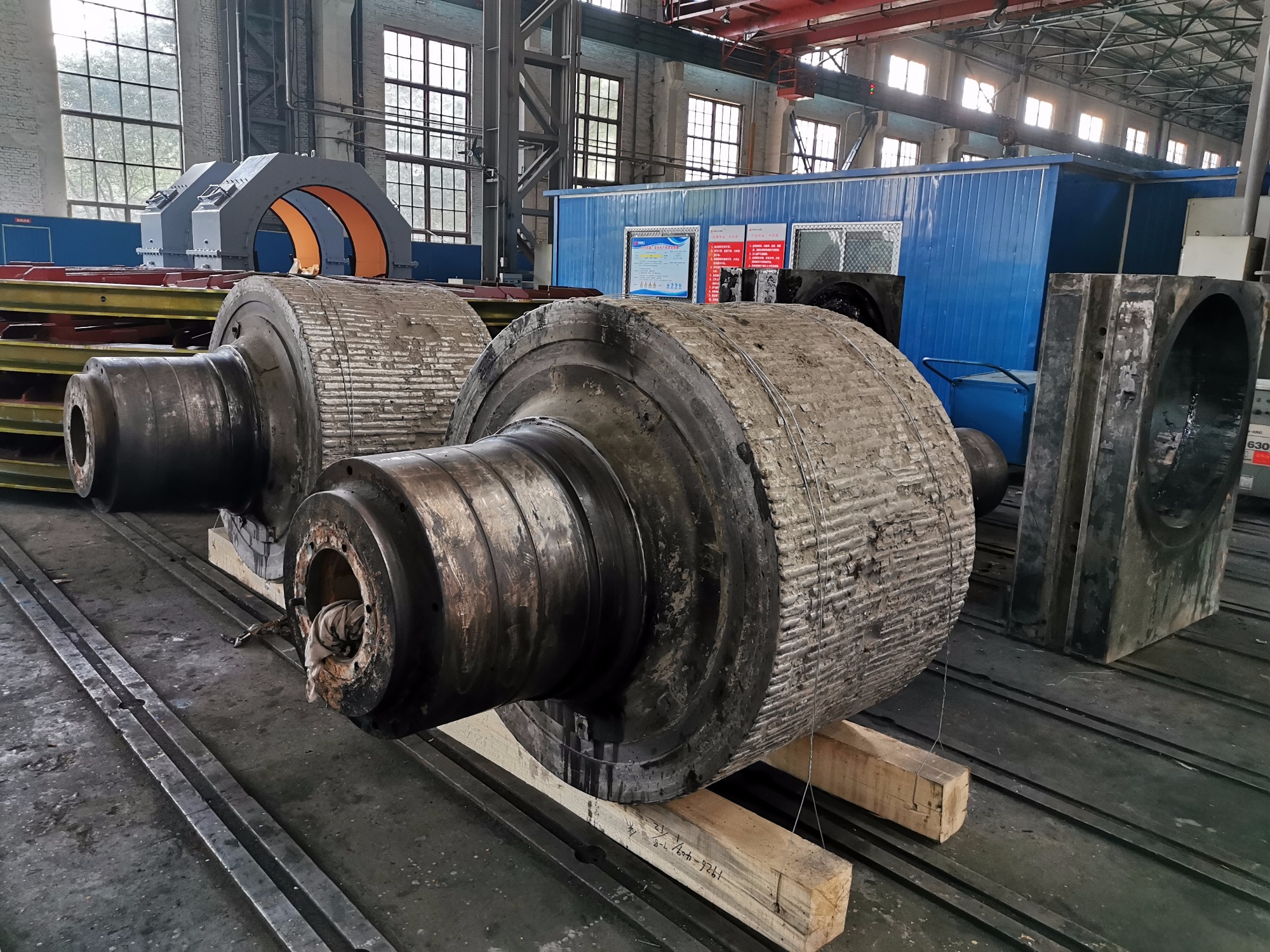 |
3.Surfacing Wear Resistant Layer of Extrusion Roll of RP180-160 High Pressure Roll Mill |
4.Extrusion Roller of High Pressure Roll Mill after use |
1.Introduction of Extrusion Roll Working Conditions of High Pressure Roll Mill
The extrusion roll is used to crush materials under high pressure on the roller press, so it is also called high pressure roll mill. The normal working pressure is 40-80 kN/cm1. Its working principle is to crush and crush the feed material into cake under high pressure when it passes through the gap between two reverse rotating rolls. During the relative rotation of the roll, the linear velocity around the roll is 1-2 m/s, which makes the extrusion roll of the roll press endure severe high stress abrasive wear and stress fatigue damage. At the same time, the damage of roll surface is complicated because foreign bodies such as metal parts often enter the crushed materials. This puts forward a high requirement for the wear resistance of the roll surface of the roller press.
Roller press is widely used in the pre-grinding and final grinding of raw cement and clinker. It has also been successfully applied in the grinding of limestone, blast furnace slag, iron ore, raw coal, gypsum, quartz sand and other materials. It has become the key main equipment in cement production. The main advantages of roller press in grinding system are to reduce power consumption and increase output. It can save 30%-50% of electricity in cement production process of grading and dispersing, and can significantly improve the production efficiency of follow-up grinder by more than 50%. It can also improve the quality of cement products with low noise. But the problem of wear of roll surface is unavoidable.
The extrusion roll of the roller press crushes the material with high pressure, so it is also called high pressure roll grinding. The normal working pressure is 40-80 kN/cm1. Its working principle is to crush and press the feeding material into cake under high pressure when it passes through the gap between two reverse rotating rolls. During the relative rotation of the roll, the linear velocity around the roll is 1-2 m/s, which makes the extrusion roll of the roll press endure severe high stress abrasive wear and stress fatigue damage. At the same time, the damage of roll surface is complicated because foreign bodies such as metal parts often enter the crushed materials. This puts forward a high requirement for the wear resistance of roll surface of roller press.
2.Failure Mechanism Analysis of Roll Surface Wear of Roller Press
Roller surface of roller press belongs to three-body abrasive wear, one fixed roll, one floating roll and high stress abrasive wear of material interaction between two rolls. Under the action of high stress, the material particles cause elastic and plastic deformation on the roll surface, and cyclic compressive stress and tensile stress will be formed at different depths of the sub-surface. When these stresses exceed the fatigue strength of the material, cracks will form on the surface. The crack will eventually lead to the flaking of the roll surface after expansion and connection. At the same time, the roll surface will also be subject to high stress cutting wear of materials and fatigue wear caused by normal stress and shear stress extrusion.
At present, the most commonly used roll materials are forgings such as Cr, W, Mo, V alloy and 45 steel. The surfacing extrusion roll has strong adaptability to abrasion resistance and working conditions, easy to use and maintain, and is widely used. The key technology of surfacing is to design the wear-resistant material and pattern of roll surface reasonably. After surfacing, the roll surface structure of surfacing material is martensite+retained austenite+acicular bainite+a small amount of carbide, the welding process is good, the crack resistance is excellent, the hardness of the pattern layer can reach HRC55-59, which has good wear resistance and toughness, thus prolonging the wear time of the roll surface and avoiding the occurrence of cracks on the roll surface.
Our roll matrix is forged entirely with high quality alloy steel. According to Hertz contact theory and pure elasticity theory, the material and hardness matching of combined anti-tear layer, transition layer and wear-resistant layer are designed scientifically according to the law of stress action. By using special surfacing material and surfacing technology, the wear resistance of roll surface has been greatly improved.Through repeated practice, the roll surface zigzag wear-resistant pattern can make the material pull-in angle more balanced and stable, and can effectively eliminate the axial force of the roll, make the equipment work more stable, and make the roll surface repair welding work more simple.